Speicher werden in der Energiewende eine zentrale Rolle spielen. Viele Jahre lang waren sie für Elektrogeräte im Einsatz. Ohne Speicher sind der Mobilfunk und andere mobile Anwendungen undenkbar. Schon länger bekommen die Speicher aber einen großen Wert für das gesamte Energiesystem. Denn dieses Energiesystem wird in Zukunft von Erzeugungsanlagen dominiert, die volatil in das Stromnetz oder auch in das Hausnetz eines Gebäudes einspeisen, aus dem sich die anderen Sektoren wie Wärme und Mobilität bedienen.
In der Regel sind es die elektrochemischen Speicher, die hier die Energiewende stützen, auch wenn Wasserstoff oder mechanische Speicher als saisonale Zwischenlager für den produzierten Ökostrom im Gespräch sind.
Die Abfallmengen steigen
Ohne Speicher wird die Energiewende in allen Sektoren nicht gelingen. Dabei geht es nicht nur um das Verschieben beispielsweise von Solarstrom in die Zeiten, in denen die Sonne nicht mehr scheint. Ein zentraler Sektor ist auch die Mobilität, bei der diese elektrochemischen Speicher zumindest mittelfristig die zentrale Rolle spielen werden. Die Anzahl an Speicherbatterien – sowohl für Elektroautos als auch für Solarenergie bis hin zur Netzstabilität – wird in den nächsten Jahren drastisch zunehmen.
Dies wirft gleich zwei Fragen auf: Gibt es genügend Rohstoffe, um die notwendige Menge an Batterien produzieren zu können? Was geschieht mit den Batterien, die ausgedient haben? Aus der Photovoltaik hat man gelernt, dass die Branche sich frühzeitig mit diesem Thema beschäftigen muss. Wobei hier ein Recycling – darauf läuft es letztlich hinaus – gleich beiden Herausforderungen begegnet. Denn einerseits beantwortet es die Frage, was mit den alten Batterien geschehen soll. Andererseits sorgt es für dringend benötigte Materialien zur Produktion neuer Batterien.
Technologien aus der Vergangenheit
Doch so einfach ist das nicht. „Denn in der Abfallwirtschaft kommen immer nur Batterien an, die in der Vergangenheit produziert und verkauft wurden. Das stellt uns vor die Herausforderung, dass wir in der Abfallwirtschaft mit Batterien umgehen müssen, die vor fünf oder zehn Jahren produziert wurden“, erklärt Roland Pomberger.
Er leitet den Lehrstuhl Abfallverwertungstechnik und Abfallwirtschaft an der Montanuniversität in Leoben. „Dazu kommt noch die Herausforderung, dass sich laufend die chemische und die Materialzusammensetzung der Batterien ändert.“
Meist ohne Kennzeichnung
Das bedeutet, dass die Abfallwirtschaft mit einer Vielfalt an unterschiedlichen Akkus zurechtkommen muss, die im Laufe der vergangenen Jahre in Umlauf gebracht wurden. Eine Kennzeichnung der einzelnen enthaltenen Materialien gibt es fast gar nicht und Schnelltests sowie eine entsprechende Datenbasis müssen erst noch aufgebaut werden.
Die Akkus sind in einem vollkommen unterschiedlichen Alterungszustand, wenn sie das Recyclingunternehmen erreichen. „Außerdem wissen die Recyclingunternehmen nicht, in welchem Ladezustand die Akkus bei ihnen ankommen“, sagt Pomberger. Das erhöht das Risiko, bei falscher Behandlung einen internen Kurzschluss und damit das thermische Durchgehen der Batterie zu verursachen. Das kann schnell zu Bränden in den Recyclinganlagen führen.
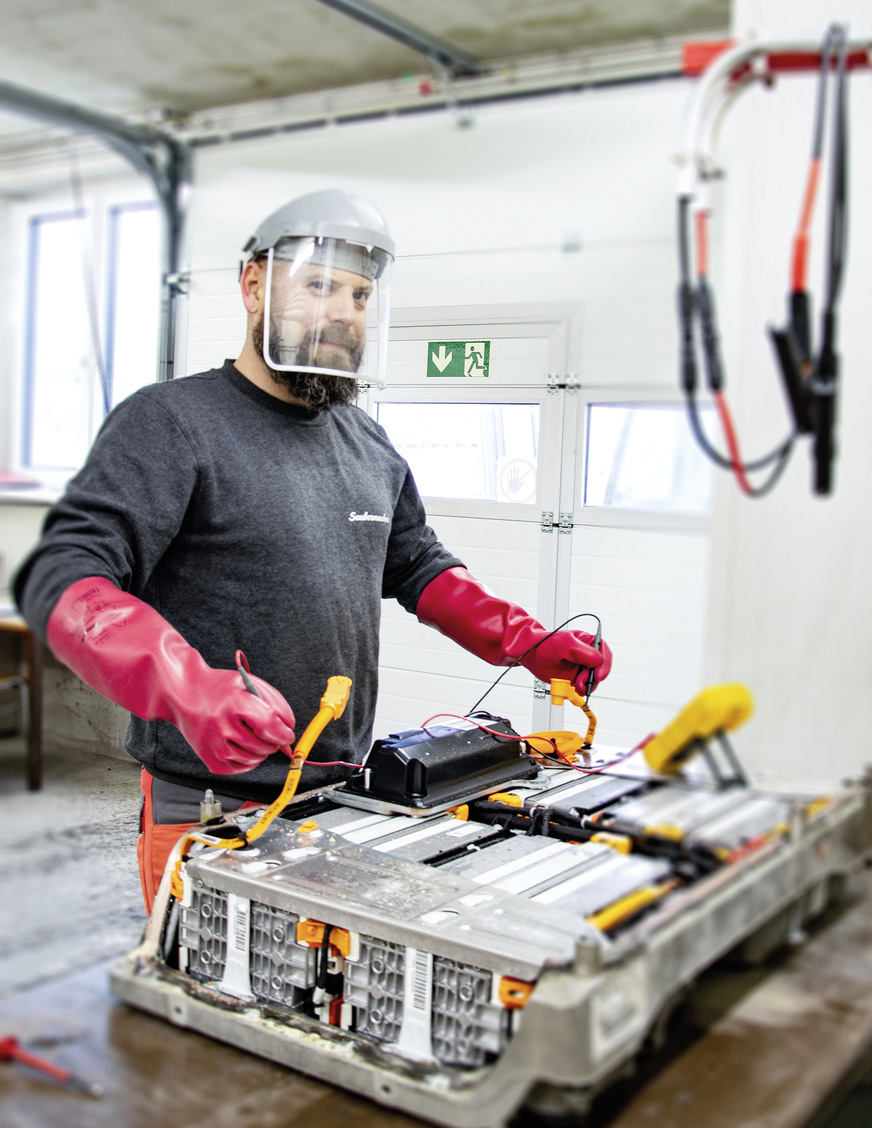
Foto: Saubermacher
Quellen sind bekannt
Selbst die Logistik vom Kunden bis zur Recyclinganlage ist nicht ganz trivial. „In diesem Bereich gab es aber in den letzten Jahren viele Entwicklungen. Es gibt neue Transportunternehmen und es gibt Entsorgungsunternehmen, die sich auf Stromspeicher – hier geht es vor allem um Lithium-Ionen-Akkus – spezialisiert haben. Der Vorteil bei der Entsorgung von stationären Solarbatterien und von Akkus in Elektroautos ist, dass die Branche zumindest weiß, wo die Lithiumspeicher sind. „Diese sind erfasst und verschwinden nicht so einfach“, sagt Pomberger.
An dieser Stelle setzen die Abfallverwerter an. Bei der Behandlung von Lithiumbatterien als Abfall haben sich zwei Methoden herauskristallisiert. Das bisher gängige Verfahren ist die pyrometallurgische Aufarbeitung. Dabei wird die Batterie eingeschmolzen. „Dieser Prozess hat Vorteile, aber auch einen Nachteil“, sagt Roland Pomberger. „Sehr viele unedle Metalle gehen in die Schlacke und können nicht verwertet werden. Dadurch werden auch die europäisch vorgegebenen Recyclingquoten nicht erreicht, da Schlacke nicht als Verwertung anerkannt ist.“
Pomberger sieht die bessere Variante in der mechanischen Aufbereitung. Dazu haben die beiden Unternehmen „Saubermacher Dienstleistung“ mit Sitz in Graz und „Redux Recyling“ einen Prozess entwickelt. In Bremerhaven haben sie eine Pilotanlage in Betrieb genommen.
10.000 Tonnen pro Jahr sind möglich
Die Anlage verarbeitet alle Arten von Lithium-Ionen-Batterien und verfügt derzeit über eine Kapazität von 10.000 Tonnen pro Jahr. Das ist die Größenordnung, in der sich der kommerzielle Betrieb einer solchen Recyclinganlage rechnet.
So viele Lithium-Ionen-Akkus fallen derzeit aber noch längst nicht an. Die Branche nennt hier Zahlen um die 3.000 Tonnen pro Jahr in ganz Europa. Doch die Mengen an alten Batterien im Rücklauf wächst derzeit im zweistelligen Bereich, wie Ralf Mittermeyr, Vorstandssprecher von Saubermacher, betont. „Mit einer Anlagenkapazität von 10.000 Tonnen pro Jahr sind wir für das absehbar steigende Mengenaufkommen weltweit jedenfalls gerüstet“, ergänzt Hans Roth, Vorsitzender des Aufsichtsrats von Saubermacher.
Aktivmaterial aufbrechen
Der dreistufige Prozess beginnt mit der vollständigen Entladung des Akkus. Der Reststrom aus den Batterien wird einfach ins Netz eingespeist. Zu diesem ersten Schritt gehört dann die mechanische Behandlung des Speichers. Das bedeutet, er wird so weit zerlegt, bis am Ende nur noch die Batteriemodule übrig bleiben. Sämtliche Gehäuseteile und die gesamte Elektronik werden entsprechend separat in den dafür gängigen Prozessen behandelt.
Im Anschluss folgt im zweiten Schritt: die thermische Behandlung der Batteriemodule mittels Pyrolyse. Das ist ein bekanntes Verfahren zur thermischen Spaltung chemischer Verbindungen. Durch die hohen Temperaturen werden die Bindungen innerhalb von großen Molekülen aufgebrochen. Dadurch wird das Aktivmaterial spröde und kann im dritten Schritt von den Folien, auf denen es aufgebracht ist, gelöst werden.
Dieser Schritt erfolgt mit klassischer Verfahrenstechnik in einem eigens für das Recycling von Lithium-Ionen-Akkus entwickelten Reaktor. Am Ende stehen Werkstoffkonzentrate zur Verfügung, die wieder in den Wertstoffkreislauf eingebracht werden. „Dabei geht es nicht um das Lithium in den Batterien und es wird noch sehr lange nicht um das Lithium gehen“, sagt Pomberger.
Wertvolles Material zurückgewinnen
Technisch ist das möglich. Wissenschaftler der Universität Clausthal haben einen Prozess entwickelt, um das Lithium in der Schlacke anzureichern, die bei der thermischen Behandlung zurückbleibt, um es so wieder zurückzugewinnen. „Doch das ist ein komplexer chemischer Prozess mit so geringen Mengen, dass dieses Verfahren in den nächsten Jahrzehnten ökonomisch nicht darstellbar ist“, weiß Pomberger.
Vielmehr geht es beim Recycling um wertvollere, weil seltenere Materialien. Auch wenn die Gewinnung und Förderung von Lithium sozial und ökologisch immer wieder umstritten ist, sind die derzeit bekannten Vorräte nach Angaben von Roland Pomberger so groß, dass die Speicherindustrie beim derzeitigen Verbrauch noch etwa 1.400 Jahre auskommen könnte.
Es geht um Kobalt, Nickel und Mangan
Selbst bei einer Verzehnfachung des derzeitigen Volumens auf 500.000 Tonnen jährlich reichen die jetzigen Lagerstätten noch für 100 Jahre aus. Das sieht bei anderen Materialien schon anders aus. Entsprechend gewinnt Saubermacher mit der Recyclinganlage für Lithium-Ionen-Akkus in Bremerhaven Aluminium, ein Aluminium-Kupfer-Gemisch, reines Kupfer und Eisen zurück. Dazu kommt noch das Aktivmaterial, in dem vor allem hochkonzentriertes Kobalt, Nickel, Mangan und eben das Lithium enthalten sind.
40 Prozent mehr als gefordert
Insgesamt stecken in den Batterien aber nur drei Prozent Lithium. Aus dem Aktivmaterial werden dann im hydrometallurgischen und pyrometallurgischen Prozess die Wertstoffe Kobalt und Nickel zurückgewonnen. Mit diesem Verfahren erreichen Saubermacher und Redux Recyclingquoten, die bis zu 40 Prozent über den europäischen Vorgaben liegen. Schon beim Start vor drei Jahren erzielte Saubermacher mit der Anlage Recyclingquoten von 60 bis 70 Prozent. Die Verbesserung des Prozesses wird in Zukunft die Recyclingquoten weiter nach oben treiben und es kommt irgendwann auch der Zeitpunkt, an dem es wirtschaftlich ist, auch die geringen Mengen an Lithium zurückzugewinnen, die in einer solchen Batterie stecken.
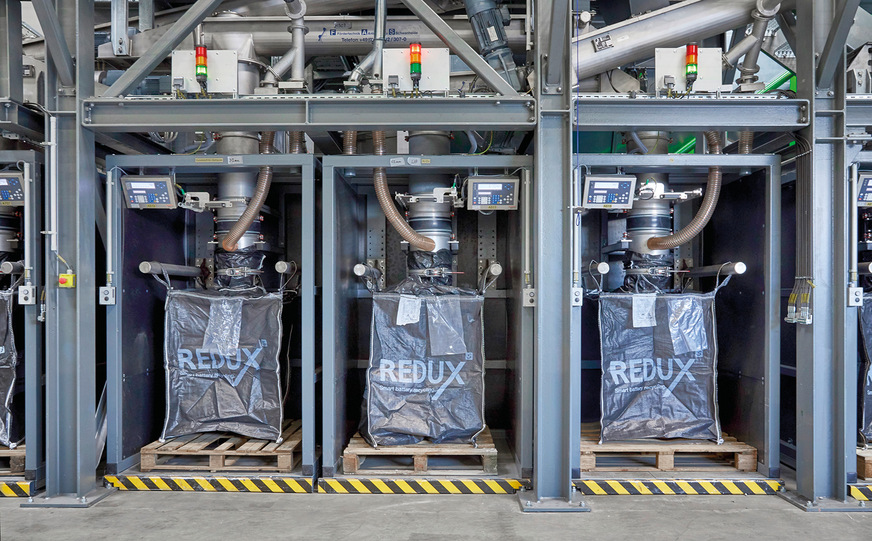
Foto: Saubermacher
Saubermacher
Alte Autobatterien kappen Stromspitze
Das Recyclingunternehmen Saubermacher hat am Standort Premstätten in der Steiermark einen sogenannten Second-Life-Speicher in Betrieb genommen. Wenn zu Arbeitsbeginn früh am Standort die Anlagen hochgefahren werden, schnellt die benötigte elektrische Leistung in die Höhe. Nach kurzer Zeit pendelt sich die Leistungsnachfrage wieder auf einem niedrigeren Niveau ein, das dann über den Tag hinweg beibehalten wird.
Diese morgendliche Spitzenlast deckt Saubermacher mit einem eigenen Batteriespeicher ab. Die Akkus für den Speicher stammen aus Elektroautos. Dort wurden sie ausgewechselt, weil sie nur noch 80 Prozent ihrer ursprünglichen Speicherkapazität erreichen und damit für die Elektromobilität ausgedient haben. Die alten Speicher aus den Fahrzeugen werden in einem aufwendigen Verfahren auf eine weitere Verwendung hin geprüft, neu vernetzt, neu verkabelt und bekommen so ein zweites Leben als stationärer Speicher bei Saubermacher.
Die Speicheranlage ist Teil eines gemeinsamen Forschungsprojekts der Grazer Energieagentur, des Speichersystementwicklers Smart Power, der Fahrzeugdienstleister AVL und AVL Ditest, von Energie Steiermark, Green Energy Lab und Saubermacher.